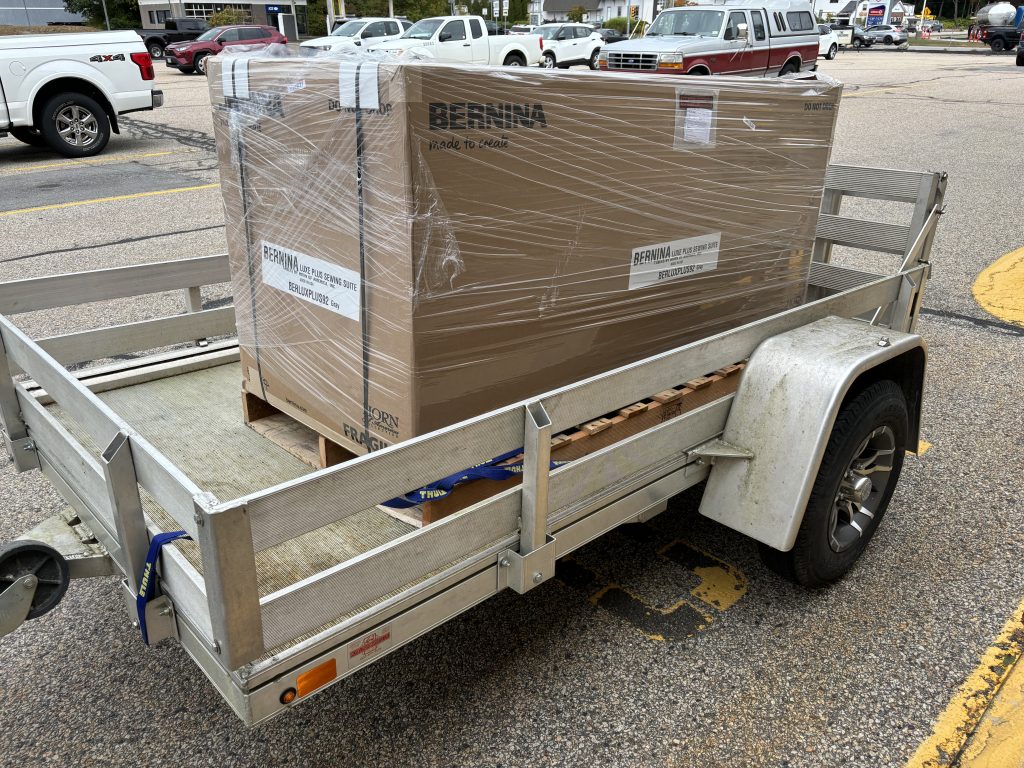
I recently purchased a new Bernina table. It is branded and sold through Bernina, but the original manufacturer is Horn. My husband and I handled moving it from the store to the sewing room. Here’s some information on our experience unboxing the table and setting it up.
For the lawyers: Note that this information is NOT officially endorsed by either Berrnina or Horn, and although everything here is correct to the best of our abilities, it is not guaranteed to be accurate or current. Read and act on this information at your own risk, we accept no responsibility for your unboxing experience.
The table arrives completely assembled, in a box strapped to a pallet. According to the shipping information, the total weight is 390 pounds. About 60 pounds of that is the pallet. It is VERY HEAVY.
We brought a couple of moving dollies, and that worked well for getting it out of the store and behind the trailer in the parking lot. Getting it onto the trailer proved to be fairly difficult, as we couldn’t roll it on. Luckily a couple of bystanders noticed our struggles and the 4 of us managed to hoist one end of it up onto the trailer, then we pushed it on from there. We strapped it down and started the 1 hour drive home. About 15 minutes later, it started to rain, so we stopped and bought a tarp, and covered the box.
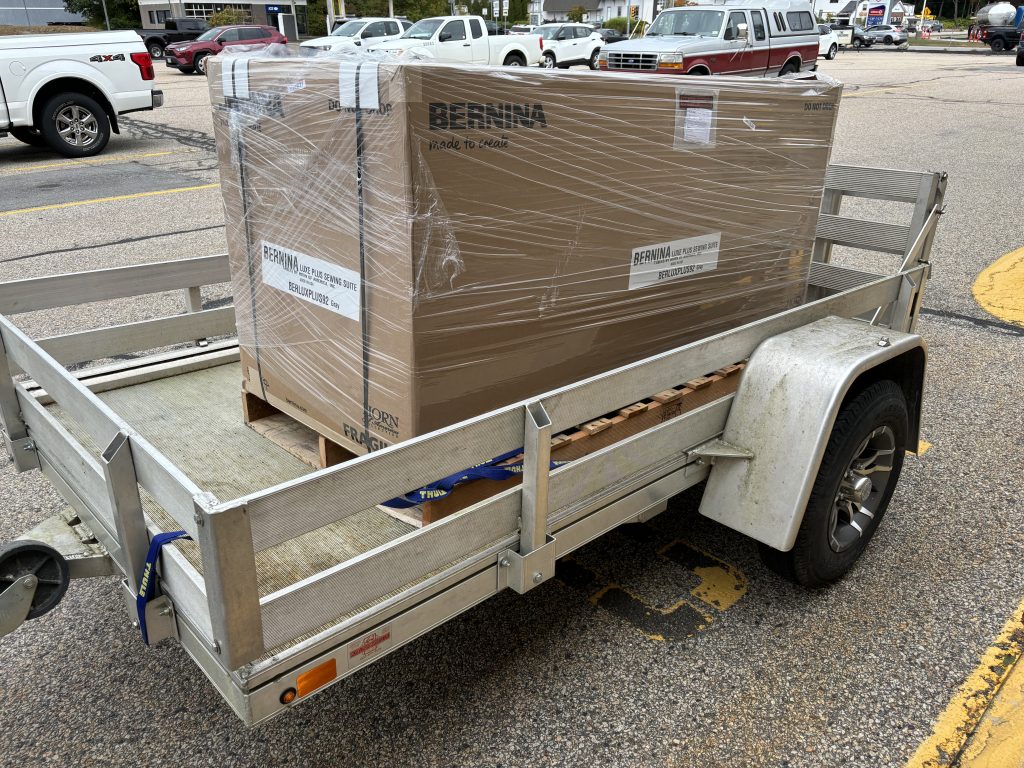
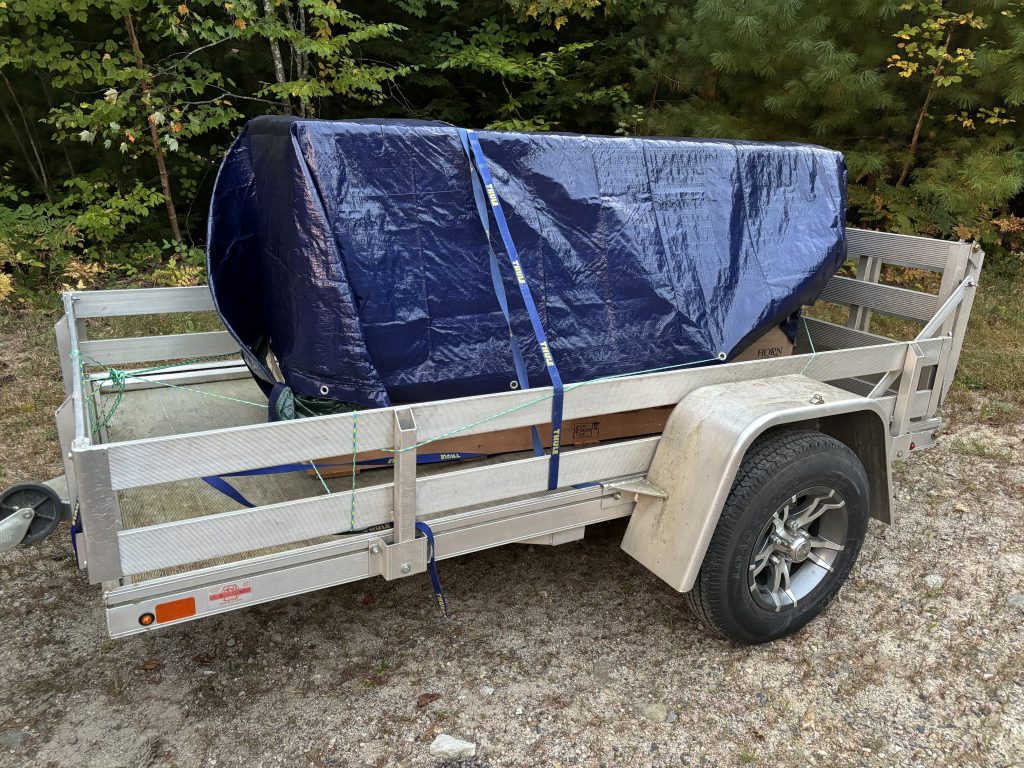
At home, getting it off of the trailer in the garage was easier because gravity was working for us. We just needed to slide it off the trailer and give it a gentle landing on the dollies. After we rolled it into position in the garage, we took the dollies out, opened the top of the box, got the instructions and started the unboxing process. Damage and missing pieces are expected to be reported within a short time of pickup, so we went ahead and unboxed it as soon as possible.
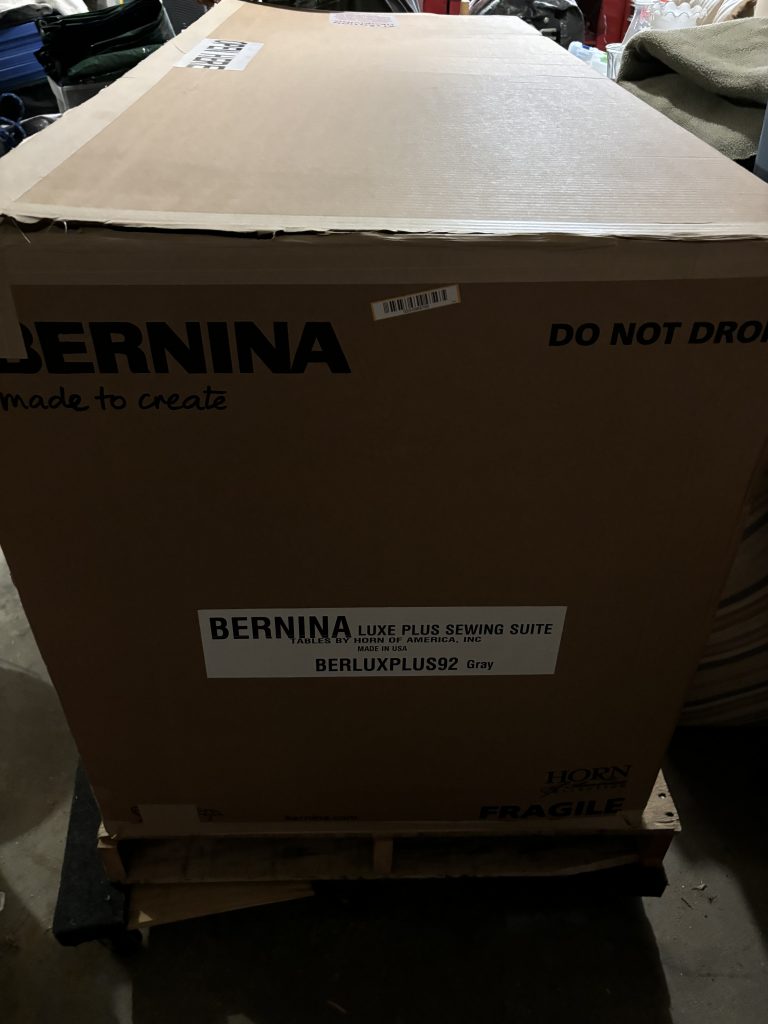
The instructions are fairly simple, but don’t go into a lot of detail. After removing it from the pallet and opening the top of the box, we discovered it was packed upside-down. The next instruction is to turn it over on its back. There was no indication what side was the back, but we figured it out after some peeking inside the box. (Hint: the long rectangular cutout is closer to the back.) Then you are to do one more turn to get it right-side up. As you can see in the picture below, there is a thick cardboard base pad that has holes in it to protect the wheels. Like the sticker says, you are supposed to leave this in place while turning it upright.
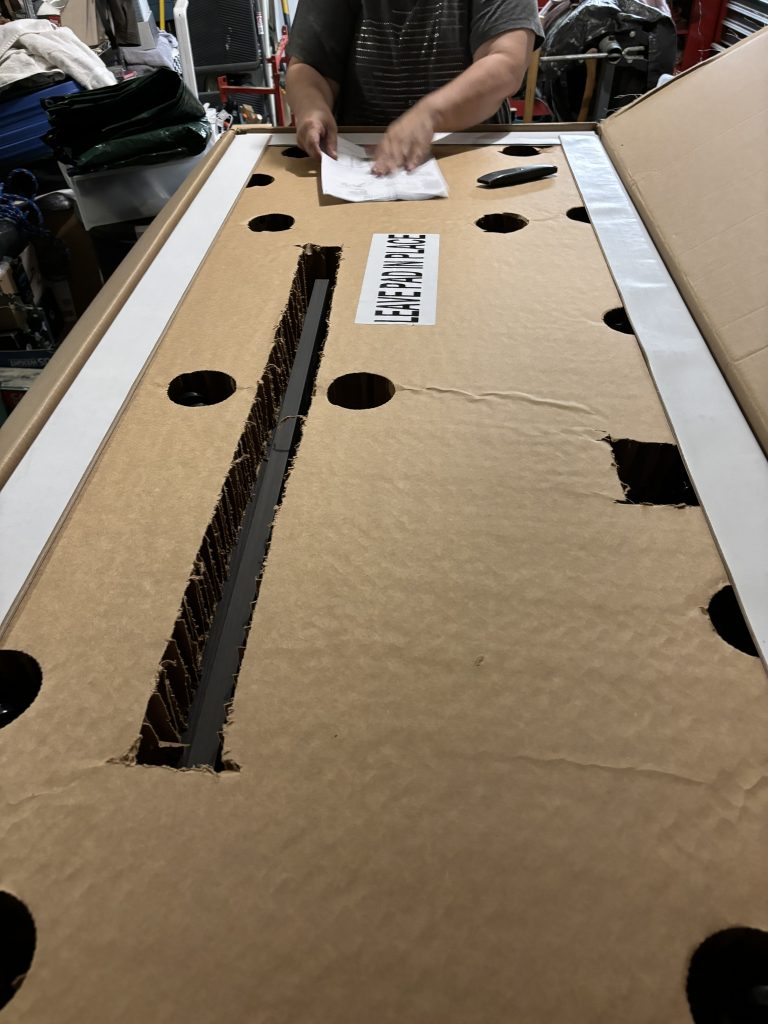
Once the table is upright, the outer box is lifted up off the table or cut off. There is some scrap wood (the tan woodgrain piece) screwed to the inner cardboard packing pieces. This packaging lifts off in one piece, revealing the table top.
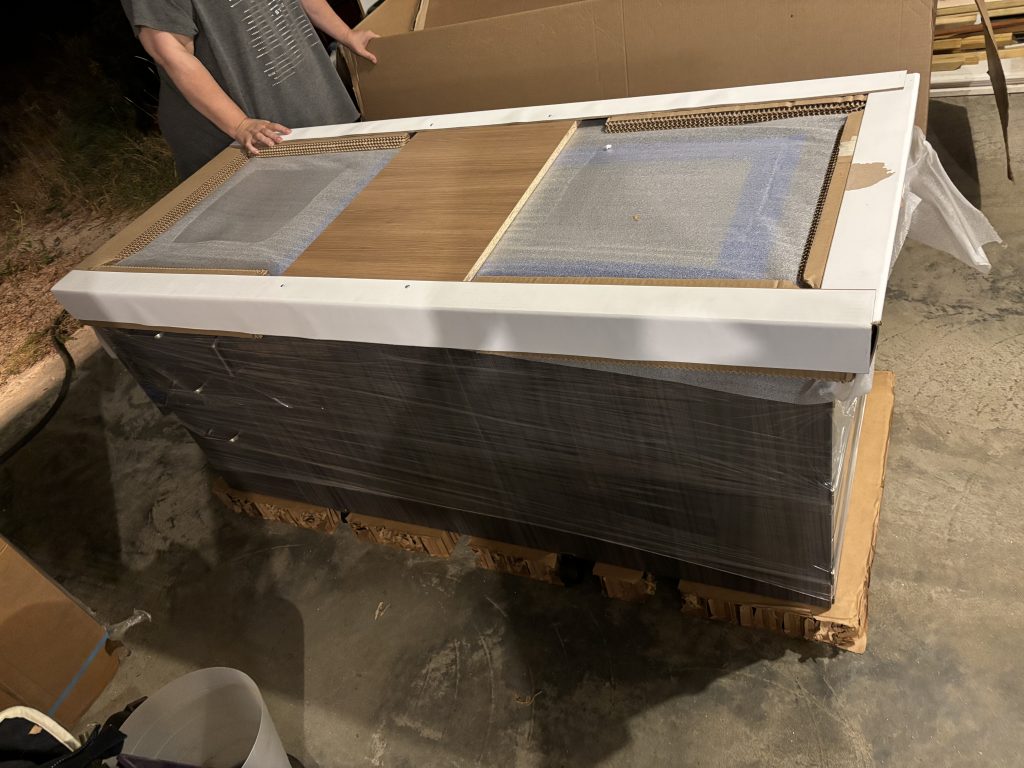
The next step of the unboxing instructions proved to be virtually impossible for us. Removing the thick cardboard base pad underneath the table. The instructions say to lift the table up, and remove the cardboard pad. The problem is that the holes are a very tight fit on the wheels, and the pad does not come off easily. This is made even more difficult if you are also trying to lift a very heavy table off the ground at the same time.
Horn, if you’re reading this, please improve this step of the process in particular. If the cardboard base was cut into 4 pieces that could be removed individually as one end or corner of the table was lifted, that might work. Requiring lifting the entire table straight up and out of the cardboard pad is an unreasonable expectation. Also, labeling the packaging to indicate what was back of the table would have been helpful when following the step to lay it on that side.
Our solution was to lay the table on its back again, remove the cardboard base, and then stand it upright again. This turned out to be a mistake. As we did this, one of the wheels had swiveled so that it was facing out. That ended up putting most of the weight of the table on that one wheel, and breaking its mounting hole in one of the table ‘wings’ in the back. Getting replacement parts has to be done through the Bernina dealer. Horn is rumored to be fairly backed up with orders for these tables currently, and they want to use all the parts they have to make new tables, so there was a very long wait to get the parts.
We then put the dollies back under the table, and rolled it into place in the sewing room without further incident. There are two shipping blocks screwed into the machine lift mechanism that must be removed before attempting to use the controls to move it.
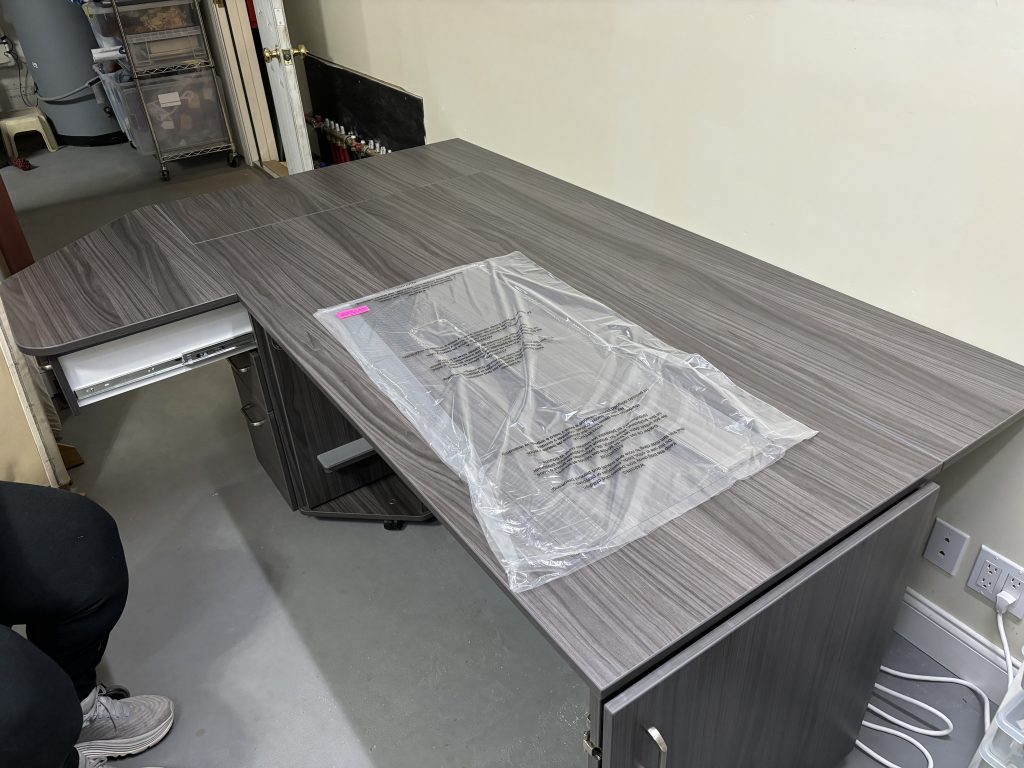
One item that ended up missing was the hoop hooks. These are 90* cup hooks with a ball on the end. They may have been somewhere in the packing materials, but if they were, we missed them. Look carefully for a small bag of 6 hooks before you get rid of the packing materials. The unboxing instructions do not mention them.
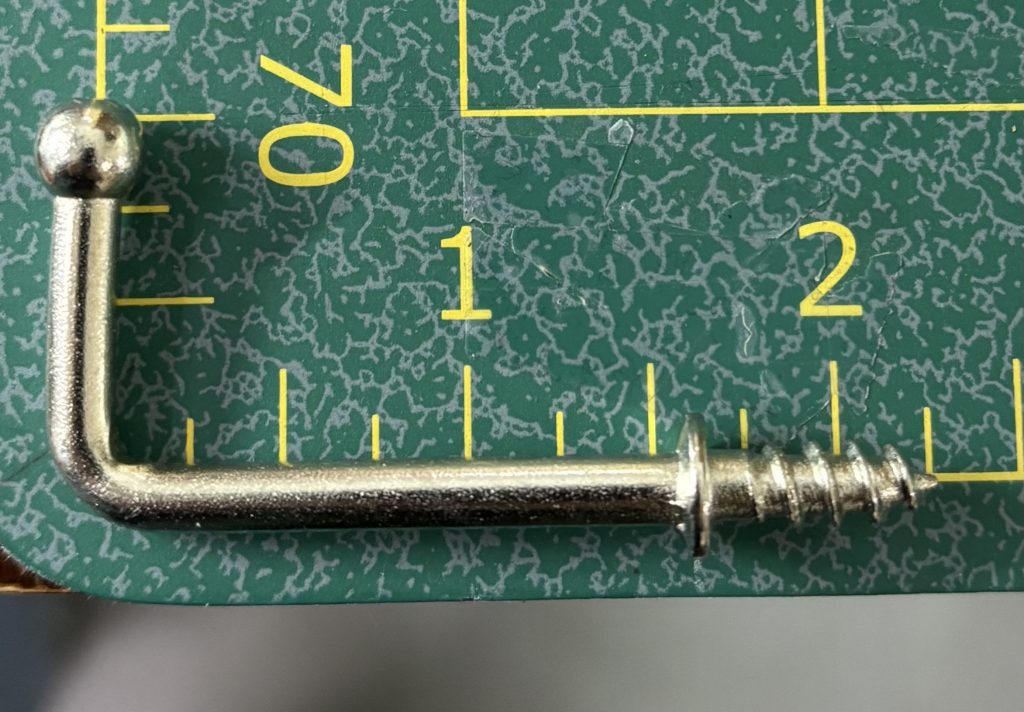
Here is the instructions and a copy of the Bill of Lading from the shipper showing the weight: